Electrical safety is our key concern and I'm always looking out for information that will help keep the industry safe. I wanted to pass along to you a report written by Professor Jim Galloway on Stray Welding Current. I hope you find it has value.
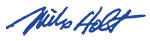
Figure 1
|
|
Figure 1
|
Electrical safety is our key concern and I'm always looking out for information that will help keep the industry safe. I wanted to pass along to you a report written by Professor Jim Galloway on Stray Welding Current. I hope you find it has value.
by Jim Galloway, B.A.Sc., C.E.T., R.S.E.
Stray Welding Currents can cause serious damage to both machinery and electrical networks and have even led to electrocutions.
If you as an electrical professional ever ask a welder to describe the electrical hook-up of an arc welding machine, the welder will most likely describe these three connections:
- The primary plug or cord connection.
- The electrode cable connected to one of the secondary output terminals. This is often referred to as the torch, electrode holder (in jargon the ˜whip' or ˜stinger'), or the gun (connected through a wire-feeder).
- The ground cable connected to the other secondary output terminal and the work or structure being welded using the ground clamp.
Perhaps then this is where the potential problems start. As an electrical professional, do you see the problem?
The Arc Welding Circuit
An electrically powered arc welding machine is essentially just an isolated step-down transformer. Depending upon the process demands the output may be rectified to DC, and there are lots of other fancy output options available such as pulsed current or variable frequency AC (however for this discussion we will just consider the basics). The welding machine then has two main secondary terminals (or studs) that make the action happen. That welding action, from an electrical professionals' perspective, is just a controlled short circuit where the secondary resistance (or impedance) is less than about ¼ of an Ohm.
Insulated copper welding cables (e.g., AWG 1/0 to 4/0) connect these two studs to the welding arc and conduct hundreds of amps in and out the machine at voltages typically in the range of 15 to 35V (under load, although the no-load terminal voltage will be higher). Arc welding machines that can provide a rated output of 250 A to 600 A are common.
The key challenge in the secondary welding circuit is to contain this large amount of current in a tight closed-loop (isolated) circuit. The electrode lead will be transmitting all of this current out to the arc but the connection to the workpiece is just as important. This leg of the circuit is properly called the workpiece lead and the connection to the work is called the return current clamp. The distinction between the grounding conductor (or protective earth) on the primary side of the machine, and the workpiece lead on the secondary side is critical. The correct set-up is illustrated in Figure 1.
Whether or not the workpiece is bonded to ground is often out of the control of the welder. A steel worktable sitting on a dry concrete floor is well isolated; that same table touching the wall of a steel-framed building is most likely at ground potential. If the weld itself is an attachment to the structure, then it will be bonded to ground. Regardless, the of concept of incorrectly calling the workpiece lead the ˜ground cable' and the return current clamp the ˜ground clamp' is firmly embedded in the welding jargon.
Stray Welding Current
When setting up a welding machine for a job there is the potential that the secondary welding current can leave the intended pathway and stray through unintended conductive paths. This is Stray Welding Current (SWC).
Often in industrial facilities these SWC events find multiple parallel conductive pathways to satisfy the circuit. They will travel through machinery bearings and gears, piping systems, ducting sheet metal, and of course electrical networks. Copper ground wires used in the electrical system are better conductors than structural steel by a factor of about 6x. Since the welding machine's transformer is isolated, all the current will be transmitted from the electrode terminal and will eventually return through the workpiece lead, but how it finds the way back can be very problematic..jpg)
Two common scenarios for SWC are illustrated in Figures 2 and 3. Figure 2 shows a case where the welder locates the return current clamp too far away from the point of welding and some of the welding current finds its way into the electrical system in a parallel pathway back to the welding machine. These pathways are solely dependent upon the resistance values of the various conductors and the connection points. Figure 3 illustrates a situation where the welder inadvertently forgets to use the workpiece lead and leaves it hanging on the welding machine. Here all the welding current returns through the electrical network, making its way back to the source through the machine's protective earth (grounding) wire and the metallic chassis to the point where the bare return current clamp is resting.
The welder in these cases could be completely unaware that hundreds of amps are damaging systems all over the plant since the performance of the welding arc would appear normal. This SWC could be arcing through critical bearings (e.g., leading to premature wear), overheating steel cable slings for rigging (e.g., leading to annealing and premature failure), arcing in hidden corners of a building (e.g., leading to fires), or overheating any of the conductors in the electrical system (e.g., leading to failure of insulation or even melted wires). One SWC event can cause extensive damage that may only be discovered at a later date, often during electrical maintenance work. In one well documented case in Ontario, Canada a maintenance welder was electrocuted when unplugging a 600V power cord due to electrical system damage caused by SWC; the welder was investigating an inoperative welding machine.
Preventing Stray Welding Current
The first step in dealing with a problem such as SWC is to clearly understand the mechanism. Conestoga College in Cambridge, Ontario was funded by a Canadian company in the green energy field to look at the welding aspects of stray current. EnerDynamic Systems Inc., was working on the problem of stray current corrosion associated with wind, solar, and battery storage DC installations. Since the problem of SWC has been known to cause significant damage in facilities and has even led to electrocutions, there was the opportunity for this collaboration.
As part of the project the college team was able to identify about a dozen plausible SWC scenarios similar to the two illustrated in Figures 2 and 3. Some of these scenarios are caused by insulation failures on welding cables, and minor internal failures in welding wire-feeders, however most of them are caused by simple errors in the placement of the return current clamp. In many cases the power cords to other electrical equipment in the vicinity of the welding operations are involved, especially if their chassis is bonded to the grounding system. Surprisingly, the overcurrent protection devices installed even in modern electrical circuits, including those protected by GFCI's, do not react to stop SWC.
To illustrate the problem the college produced educational videos demonstrating how SWC occurs and the sort of damage that will happen to a welding machine's power cord. If welders are always diligent about making certain that welding cables are properly sized and that the return current clamp is placed as close as feasible to the point of welding, most cases of SWC would be solved. Unfortunately the idea that the workpiece lead is a ˜ground cable' has led to the belief that attaching it at any convenient spot to get ground is acceptable, especially when doing so would avoid the necessity to drag two long heavy cables, the electrode lead and the workpiece lead, to a remote weld location instead of just one electrode lead.
Conestoga College helped design a variation of a patent pending Stray Current Interrupter Device (SCID) for welding applications based upon the input of students and faculty from the Energy Systems Engineering Technology and the Welding Engineering Technology programs. A video showing a prototype SCID acting as an engineering control device and preventing SWC is also available.
Summary
The high currents associated with arc welding operations can cause extensive damage to electrical systems and machinery if they stray from the designed closed-loop secondary circuit. Electrical professionals need to be aware of how Stray Welding Current occurs, and how easily it can cause severe damage, especially to the various protective earth conductors in the vicinity of welding operations.
The first step towards preventing SWC is to educate everyone involved about the proper terminology and the importance of locating the workpiece lead (and the return current clamp) as close as possible to the location of the weld. The workpiece lead is not a ˜ground' conductor.
Conestoga College in Cambridge, Ontario has made videos freely available on their YouTube Channel for anyone to view and learn more about the problem of SWC (see Video Links below).
About the Author
Jim Galloway, B.A.Sc., C.E.T., R.S.E, is a Professor of Welding Engineering Technology at Conestoga College in Cambridge, Ontario . He also volunteers as a technical member on several Canadian Standards Association committees including CSA W117.2 - Welding Safety and CSA C232(CSC26) - Electric Welding Equipment.
Video Links:
|