For EC&M Magazine
By Mike Holt, NEC® Consultant
Here's the follow-up to yesterday's newsletter.
This includes the answers to the questions sent, so you can see how you did.
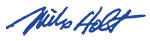
Figure 01
|
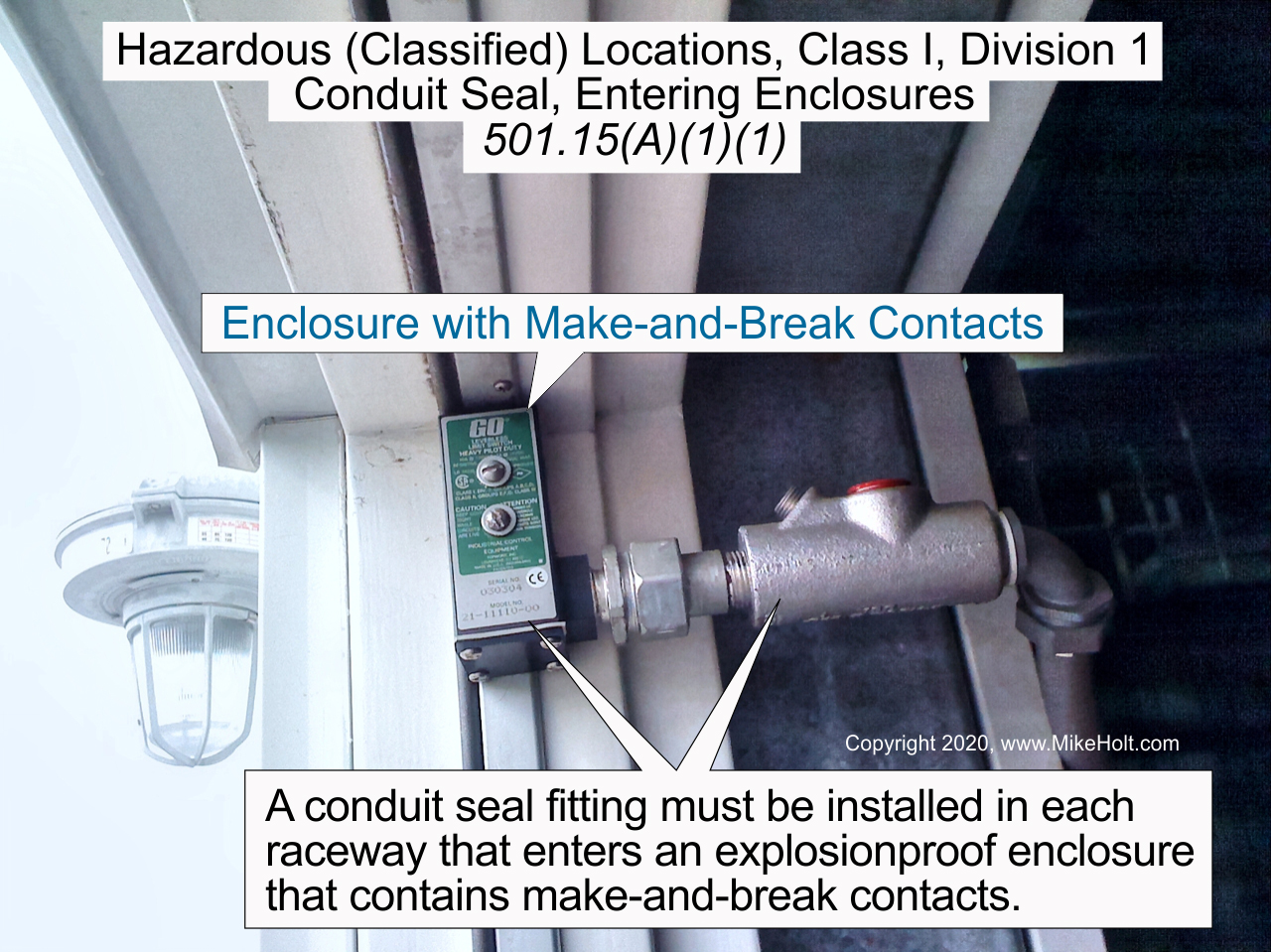 |
Figure 01
|
For EC&M Magazine
By Mike Holt, NEC® Consultant
Here's the follow-up to yesterday's newsletter.
This includes the answers to the questions sent, so you can see how you did.
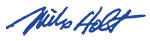
Note: The answers to these questions are based on the 2020 NEC.
Q1. What is the NEC requirement for ground-fault detection of storage battery circuits?
A1. Battery circuits exceeding 100 volts between the conductors or to ground are permitted to operate with ungrounded conductors, provided a ground- fault detector and indicator is installed to monitor for ground faults [480.13].
Q2. What is the Code requirement for documentation of hazardous (classified) locations?
A2. All areas designated as hazardous (classified) locations must be properly documented. The documentation must be available to those who are authorized to design, install, inspect, maintain, or operate the electrical equipment [500.4].
Author's Comment
â–ºProper documentation of hazardous areas assists the designer, installer, and authority having jurisdiction in ensuring adherence to the stringent requirements contained in Articles 501 through 517 of the Code.
â–ºTo assist in compliance with the above requirements, some authorities having jurisdiction require drawings that indicate hazardous (classified) location areas and their classification(s).
â–ºThe NEC does not classify specific hazardous (classified) locations in Articles 511 through 517, unless identified as such in the articles. Determining the classification of a specific hazardous area is the responsibility of those who understand the dangers of the products being used, such as the fire marshal, plant facility engineer, or insurance underwriter. It is not the responsibility of the electrical designer, electrical contractor, or electrical inspector. Before performing any wiring in or near a hazardous (classified) location, contact the plant facility and design engineer to ensure that proper installation methods and materials are used.
Be sure to review 500.4(B) for additional standards that might need to be consulted.
Q3. What techniques does the Code require for the protection of electrical and electronic equipment in hazardous (classified) locations?
A3. Electrical and electronic equipment in hazardous (classified) locations must be protected by one or more of the following techniques [500.7]:
(A) Explosionproof Equipment. Explosionproof equipment is permitted in any Class 1 location for which it is identified.‚
Author's Comment
â–ºExplosionproof equipment is designed to be capable of withstanding and containing the force of an internal explosion, and the hot gases within the enclosure cool as they escape [Article 100].‚
(B) Dust-Ignitionproof Enclosures. Dust-ignitionproof enclosures are permitted in any Class II location.‚
Author's Comment
â–ºDust-ignitionproof enclosures are designed to exclude dusts and will not permit arcs, sparks, or heat within the enclosure to cause the ignition of exterior dust [Article 100].
(C) Dusttight Enclosures. Dusttight enclosures are permitted in Class II, Division 2 or any Class III location.
(D) Purged and Pressurized Systems. Purged and pressurized systems are permitted for equipment in any hazardous (classified) locations for which they are identified.
(I) Oil-Immersed Contacts. Oil-immersed make-and-break contacts can be installed in a Class I Division 2 location.
(J) Hermetically Sealed Contacts. Can be installed in Class I, Division 2; Class II Division 2; or Class III, Division 1 and 2 locations.
Author's Comment
â–ºHermetically Sealed is when equipment is sealed against the entrance of an external atmosphere where the seal is made by methods such as soldering, brazing, welding, or the fusion of glass to metal [Article 100].
Q4. What does the Code require for raceway and cable seals in Class I locations?
A4. Seals for raceway and cable systems must comply with 501.15(A) through (F) [501.15].
Note 1: Raceway and cable seals must be installed to:‚
- Minimize the passage of gases and vapors from one portion of electrical equipment to another through the raceway or cable.
- Minimize the passage of flames from one portion of electrical equipment to another through the raceway or cable.
- Limit internal explosions to within the explosionproof enclosure.
(A) Raceway Seal”Class I, Division 1. In Class I, Division 1 locations, raceway seals must be located as follows:
(1) Entering Enclosures. A raceway seal is required in each raceway that enters an explosionproof enclosure if either (1) or (2) apply:
(1) If the explosionproof enclosure contains make-and-break contacts. Figure 01
Ex: A raceway seal is not required if the make-and-break contacts are:
(1) Within a hermetically sealed chamber.‚
(2) Immersed in oil in accordance with 501.115(B)(1)(2).
(3) Contained within an enclosure that is marked Leads Factory Sealed, Factory Sealed, Seal not Required, or the equivalent.
Q5. What wiring methods are acceptable to the NEC in Class II division 1 locations?
A5. The following wiring methods can be installed in a Class II, Division 1 location [502.10 (A)]:‚
(1) Threaded rigid metal conduit (Type RMC) or threaded intermediate metal conduit (Type IMC).
(2) Type MI cable terminated with fittings that are listed for the location.
(3) In industrial establishments with restricted public access where only qualified persons will service the installation, MC‘HL cable listed for use in Class II, Division 1 locations with a gas/vaportight continuous corrugated metallic sheath, an overall jacket of suitable polymeric material, a separate equipment grounding conductor(s) sized in accordance with 250.122, based on the rating of the overcurrent protective device, and terminated with fittings that are listed for the location.
(4) Types OFNP, OFCP, OFNR, OFCR, OFNG, OFCG, OFN, and OFC optical fiber cable can be installed in raceways [502.10(A)] and must be sealed in accordance with 502.15.
(2) Flexible Connections. If flexibility is necessary, any of the following wiring methods are permitted in a Class II, Division 1 location:‚
(1) Dusttight flexible connectors.
(2) Liquidtight flexible metal conduit, (Type LFMC), with listed fittings.
(3) Liquidtight flexible nonmetallic conduit, (Type LFNC), with fittings that are listed.
(4) Interlocked armor Type MC cable with an impervious jacket and termination fittings that are listed for Class II, Division 1 locations.
(5) Flexible cords listed for extra-hard usage, containing an equipment grounding conductor and terminated with listed dusttight flexible cord connectors. The flexible cord must be installed in accordance with 502.140.
(3) Boxes and Fittings. Boxes and fittings must be provided with threaded bosses and must be dusttight. Boxes and fittings in which taps, joints, or terminal connections are made, or used in locations where dusts are of a combustible, electrically conductive nature [500.6(B)(1) Group E], must be identified for Class II locations.‚
|